Реклама на retail.ru
на новости ритейла
Получайте новости
индустрии ритейла первым!
Поделиться
Производитель мебели «Альтернатива» на 20% увеличил скорость исполнения заказа и сократил брак в 3 раза
Производитель мебели на заказ автоматизировал процессы упаковки и отгрузки и внедрил систему планирования. Это было необходимо, так как при сборке и отгрузке сложной мебели с большим количеством деталей и сборных конструкций часто возникали ошибки, бывали случаи пересорта и недокомплектации. Покупателям приходилось ждать недостающих элементов, росло количество рекламаций, компания несла дополнительные расходы. В результате автоматизации получен эффективный инструмент управления производством. Уже через три месяца после внедрения скорость выполнения заказа выросла на 20%, рекламационный брак снизился в 3 раза, ошибки при отгрузке, пересорт и недокомплект полностью ликвидированы. Для автоматизации была выбрана система 1С:Управление нашей фирмой (1С:УНФ). В этом кейсе мы подробно рассмотрим особенности автоматизации мебельного производства и расскажем, на какие моменты стоит обратить внимание.
Мебельная компания «Альтернатива» производит корпусную и встроенную мебель с 2013 года. На сегодняшний день является одним из лидеров сектора по проектированию и производству мебели по индивидуальным заказам в городе Кузнецке. Компания производит более 400 заказов в месяц и реализует продукцию через дилерскую сеть на всей территории России
Производство мебели по индивидуальным проектам сложно представить без автоматизации. Особенностью такого производства является учет персональных требований клиентов, которые отражаются в индивидуальных эскизах. Эскизы разрабатываются и проектируются в специализированных программах. Соответственно, заказы отличаются размерами, материалами, фурнитурой и цветом.
По мере роста производства текущие бизнес-процессы начинают давать сбои — растет количество ошибок и увеличивается срок исполнения заказа. Значительную часть времени приходится уделять не развитию бизнеса, а исправлению этих ошибок, разбору причин и поиску ответственных. На этом этапе стоит задуматься об использовании современных автоматизированных систем управления, которые проконтролируют операции и помогут оперативно принимать управленческие решения в сложных случаях.
Бизнес-процессы до автоматизации
На старте работ компания использовала «самописную» программу, которая не позволяла решать задачи бизнеса.
Технологический процесс изготовления мебели по индивидуальным эскизам включает следующие операции:
-
раскрой листов ЛДСП в соответствии с картами раскроя на заготовки;
-
кромление заготовок — облицовка кромок заготовок;
-
сверление отверстий под фурнитуру — присадка отверстий.
Завершается процесс сборкой необходимых элементов, проверкой качества, упаковкой и передачей на склад готовой продукции для последующей отгрузки покупателю.
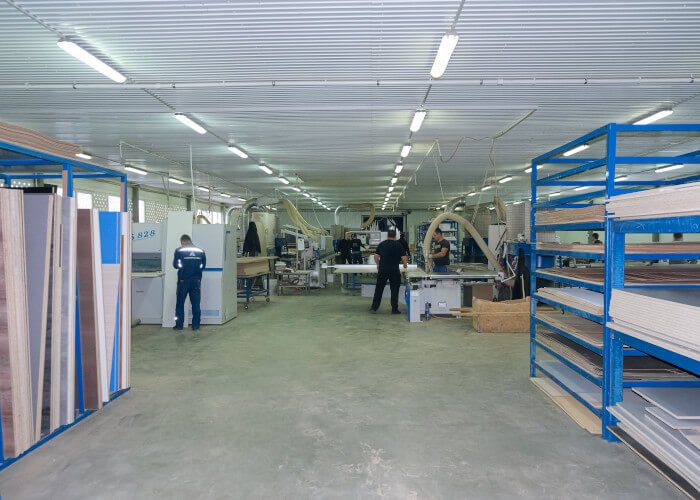
Производство мебельной компании «Альтернатива»
«Узкие места»
В списке слабых мест большинства мебельных компаний оказываются процессы упаковки и отгрузки. Рассмотрим подробнее, как были организованы данные процессы в компании.
После выполнения заключительной производственной операции, детали заказов, разделяли на две категории: простые детали и детали для сложных конструктивных элементов.
Простые детали — не требуют сборки, их привозили на участок упаковки на специализированных тележках. Сотрудники проводили контроль качества деталей и упаковывали их в гофрокартон, указав на упаковке соответствующий номер заказа маркером. Номер позволял идентифицировать упаковки при отгрузке заказа. Упаковки отвозили на склад готовой продукции, с которого отгружали покупателю.
Сложные конструктивные элементы — детали заказа, которые требуют сборки до момента отгрузки. Детали для сложных конструктивных элементов передаются на специализированный участок, где происходит сборка этих элементов. После сборки они не отвозятся на участок упаковки, а упаковываются непосредственно на участке сборки, и передаются на склад готовой продукции.
Часто возникали ситуации, когда при отгрузке ответственный сотрудник не знал о наличии сборных конструкций и не мог своевременно отгрузить все составляющие заказа — часть деталей оставалась на участке сборки. Кроме того, нередки были случаи пересорта по деталям и упаковкам. Клиентам приходилось ждать отгрузки недостающих элементов, а компания несла дополнительные расходы.
С ростом объёма производства росло и количество ошибок, следовательно, увеличивались рекламационные обращения клиентов. Внедрение системы оперативного контроля на участках позволило бы решить проблему.
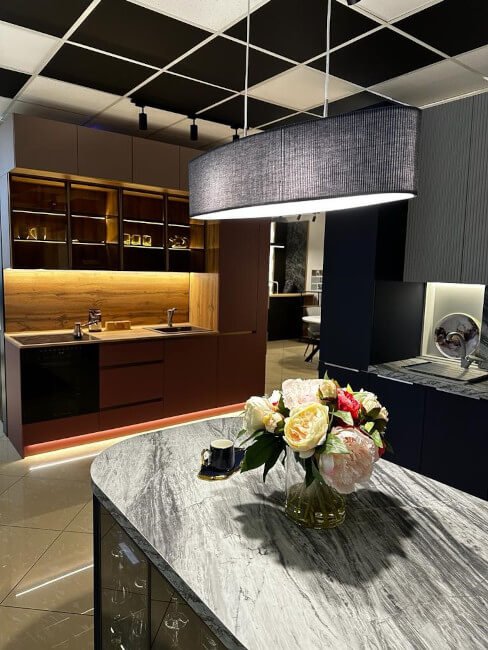
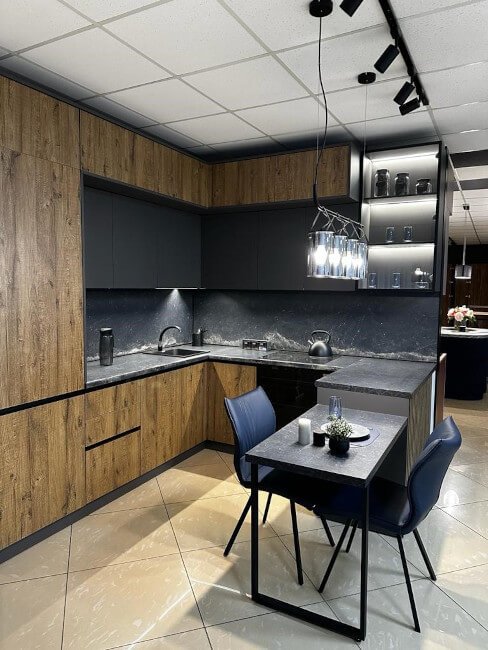
Рациональный подход к внедрению инструментов бережливого производства
При выборе партнера по автоматизации «Альтернатива» обратилась к компании С5, имеющей опыт работы с мебельными компаниями. А значит погружение в бизнес-процессы не займет много времени. Автоматизацию решено было начать с анализа «узких мест».
«Чтобы максимально исключить влияние человеческого фактора на процессы, при автоматизации решено было руководствоваться инструментами бережливого производства — методом Пока-Йоке. Суть данного метода в поиске и предотвращении возможных ошибок до их совершения», — рассказал Андрей Коромыслов, руководитель компании С5.
В основу автоматизации процессов упаковки и отгрузки легли следующие принципы:
-
Анализ причин: ошибочные действия должны предотвращаться на месте, прежде чем они приведут к рекламациям.
-
Сплошной контроль: необходимо создать инструмент, который обеспечит контроль любой детали и упаковки в разрезе каждого заказа.
-
Немедленные меры по исправлению: промежуток времени от обнаружения ошибки до её исправления должен быть минимален.
Итак, осталось реализовать все в 1С. Поскольку в программе 1С:УНФ реализована часть требуемых инструментов, решено было все дальнейшие доработки проводить на базе 1С:УНФ. Сильным преимуществом программы 1С стала возможность доработать функционал под индивидуальные задачи производителя и интегрировать имеющиеся программы проектирования и раскроя мебели, создавая комплексную автоматизированную систему. Было автоматизировано 30 рабочих мест.
Первый этап автоматизации. Разработка и внедрение механизмов «защиты от ошибок»
Первым шагом — реализовали интеграцию программы для проектирования и 1С:УНФ для выгрузки деталей и фурнитуры в систему. Это позволило подгружать в систему документацию по заказу, подготовленную технологами, и определять себестоимость изделия до момента запуска в производство, исключив ошибки в ценообразовании.
Вторым шагом — внедрили систему штрихкодирования деталей и упаковок для их идентификации в системе и фиксации этапа производства заказа. Приобрели беспроводные сканеры штрихкодов и принтеры этикеток.
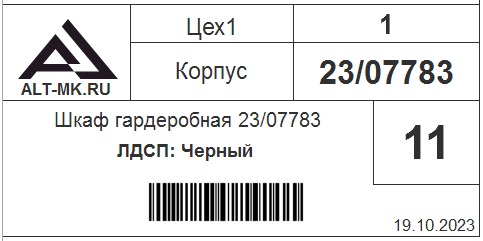
Этикетка для упаковок
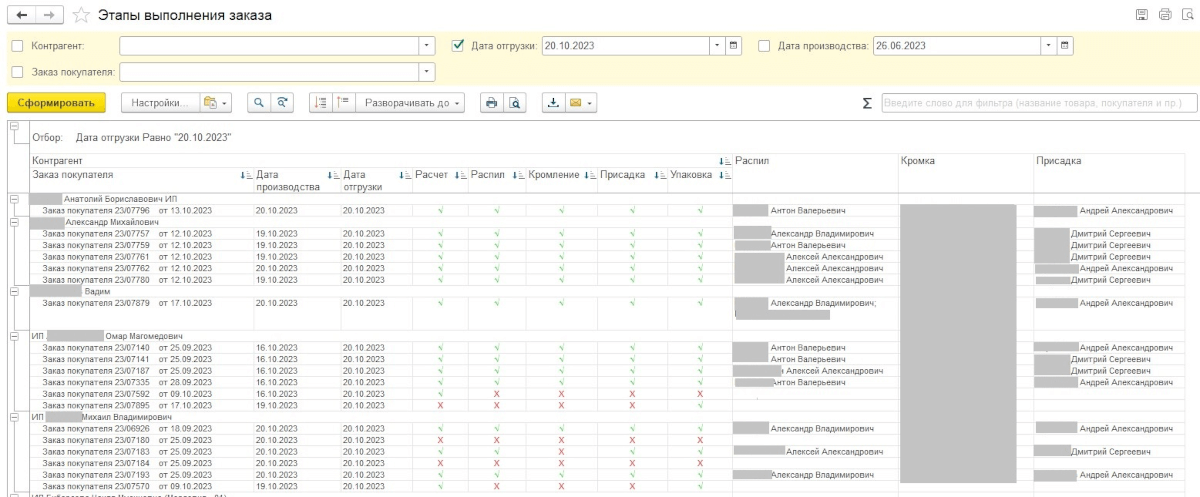
Вариант отчета, отражающий этапы выполнения заказа и ответственных за выполнение лиц
Третьим шагом — организовали АРМ для упаковщиков и кладовщиков. Для комфорта и прозрачности процесса закупили мониторы на участок отгрузки.
В результате производитель мебели получил надежный инструмент предотвращения брака поставки.
Ликвидация «узких мест»
Так теперь происходит упаковка деталей с использованием системы контроля в 1С:УНФ:
-
Необходимо войти в систему и открыть документ «Упаковка №NN» соответствующего заказа.
-
Отсканировать штрихкод на деталях заказа, которые планируется уложить в одну упаковку.
-
Завершить процесс и распечатать этикетку на соответствующую упаковку.
В программе упакованные детали будут закрашиваться зеленым цветом. В случае, если сотрудник совершает ошибку, например, сканирует деталь, которая не относится к текущему заказу — система сообщает об этом. Доступ к печати этикетки закрыт до устранения ошибок. Если по заказу остались неупакованные детали, а процесс упаковки завершается, программа также выдаёт предупреждение и отражает детали, которые необходимо упаковать. Таким образом, создать упаковку с деталями разных заказов невозможно. Процедуру внедрили на всех участках, где проводится упаковка.
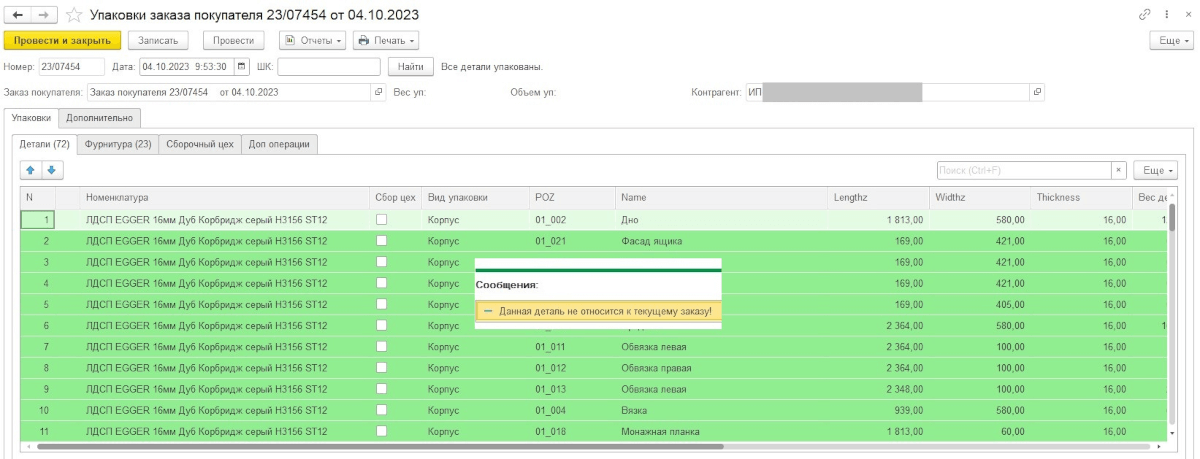
Документ «Упаковки заказа покупателя», на основании которого проводится контроль полноты и комплектности упаковки заказа
Похожий механизм внедрили и на этапе отгрузки. Рассмотрим его подробнее.
Для старта процедуры отгрузки кладовщик сканирует упаковочный лист. На экране монитора сотрудника отображается перечень упаковок, которые необходимо отгрузить клиенту. Упаковки, которые необходимо вынести из цеха в машину, сканируются. На экране монитора фиксируется текущее состояние процесса — сколько упаковок отгружено и сколько осталось отгрузить.
Программа производит проверку соответствия упаковок отгружаемым заказам и выдаёт предупреждающий сигнал в случае попытки отгрузить упаковки сторонних заказов. Отгрузку можно продолжить только после устранения ошибок. Система не даст завершить отгрузку и распечатать необходимые документы до тех пор, пока все упаковки не будут отсканированы, а ошибки устранены. За исключением случаев, когда частичная отгрузка предусмотрена.
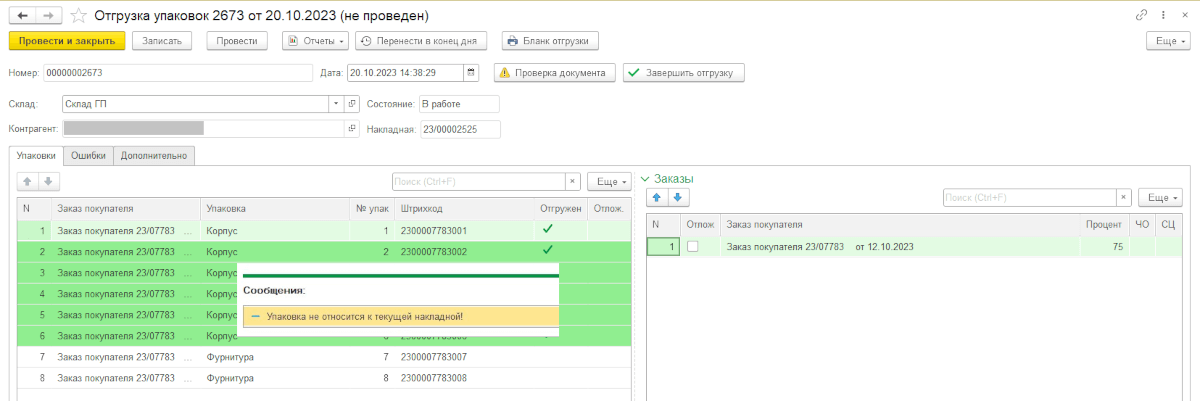
Документ «Отгрузка упаковок», на основании которого проводится контроль полноты и комплектности отгрузки заказов
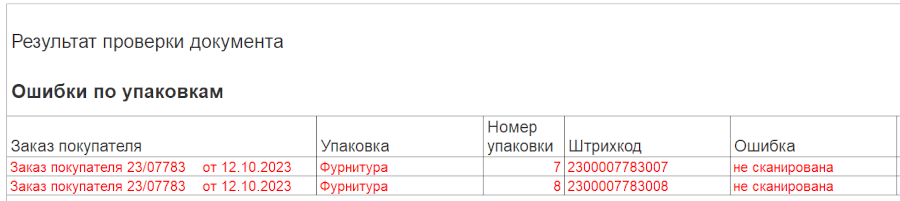
Результат проверки на ошибки в процессе отгрузки
Анализ отклонений как инструмент гибкой системы контроля
Для контроля ошибок производственного характера в большинстве компаний предусмотрены отделы контроля качества. Если ответственные сотрудники обнаружили недостатки — компания направляет усилия на их устранения. Но бывает, что клиент готов забрать заказ частично, а недостающие элементы принять в составе следующих отгрузок. В таких случаях важно иметь гибкую систему контроля. А также отслеживать частоту и причины возникновения таких ситуаций для внесения дальнейших корректировок в производственный процесс.
Мы предусмотрели вариант частичной отгрузки — неполной отгрузки упаковок или деталей, которая происходит по вине производства. Таким образом дополнительно сформировали инструмент для анализа причин неполной отгрузки и разработки системных корректирующих мероприятий.
Кроме того, мы предусмотрели механизм подготовки к отгрузке, когда ответственное лицо заблаговременно проверяет наличие всех упаковок по заказам на складе готовой продукции. В случае их отсутствия, определяет неупакованные детали, их местонахождение и корректирует процесс.

Инструмент подготовки к отгрузке заказов.
Итоги первого этапа
В результате первого этапа компания получила надежный инструмент контроля процессов упаковки и отгрузки. Система проверяет корректность операций, предупреждает о совершении ошибок и блокирует дальнейшие действия до момента их устранения. Когда все проверки пройдены, система открывает доступ к печати отгрузочных документов, включая отгрузочную ведомость, в которой отражается состав и комплектность заказов.
Второй этап автоматизации
Сокращение потерь путем внедрения производственного планирования
На втором этапе наводили порядок в области организации управления производством. «Нам важно было понимать, насколько загружено производство, и как планировать выпуск вновь взятых заказов. Требовался инструмент, который позволил бы распределять работы по участкам и ответственным, а также оценивать их исполнение с точки зрения полноты и своевременности», — прокомментировал Андрей Коромыслов.
Первым шагом определились с максимально допустимой дневной загрузкой производства. С учетом этого настроили в системе механизмы, позволяющие на этапе оформления заказа автоматически планировать дату выпуска продукции исходя из текущей загрузки производства.
Вторым шагом разработали АРМ для начальника производства, мастеров участков Корпусного цеха, цеха Фасадов и других подразделений. Теперь они могут планировать и оценивать загрузку этих подразделений на конкретный период с учетом приоритетности заказов. Разработали инструмент контроля исполнения работ на участках (в подразделениях) в разрезе временных интервалов. Кроме того, разработали механизм формирования производственных заданий по сотрудникам и оценки их загрузки на конкретный период времени.
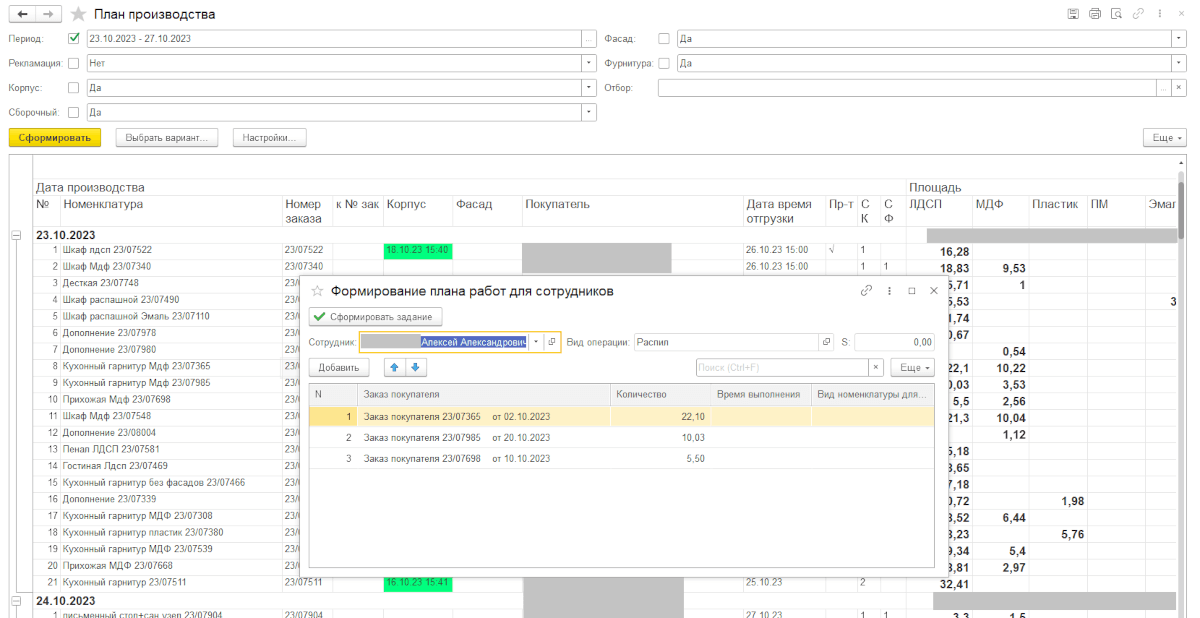
Процесс «Формирование плана работ для сотрудников», с помощью которого мастера участков из плана производства распределяют работы по сотрудникам
От работников производства не было сопротивления скорректированному бизнес-процессу. Они получили инструмент оперативной отметки выполнения работ. Достаточно отсканировать свой личный штрихкод и штрихкод любой детали заказа, чтобы программа зафиксировала выполнение операции. Данный механизм не только избавил сотрудников от дополнительной «бумажной работы», но и упростил задачу бухгалтерии в области расчета сдельной заработной платы. Теперь зарплата рассчитывается в автоматическом режиме. Кроме того, процесс стал полностью прозрачным — фиксируются исполнитель и работы по заказу.
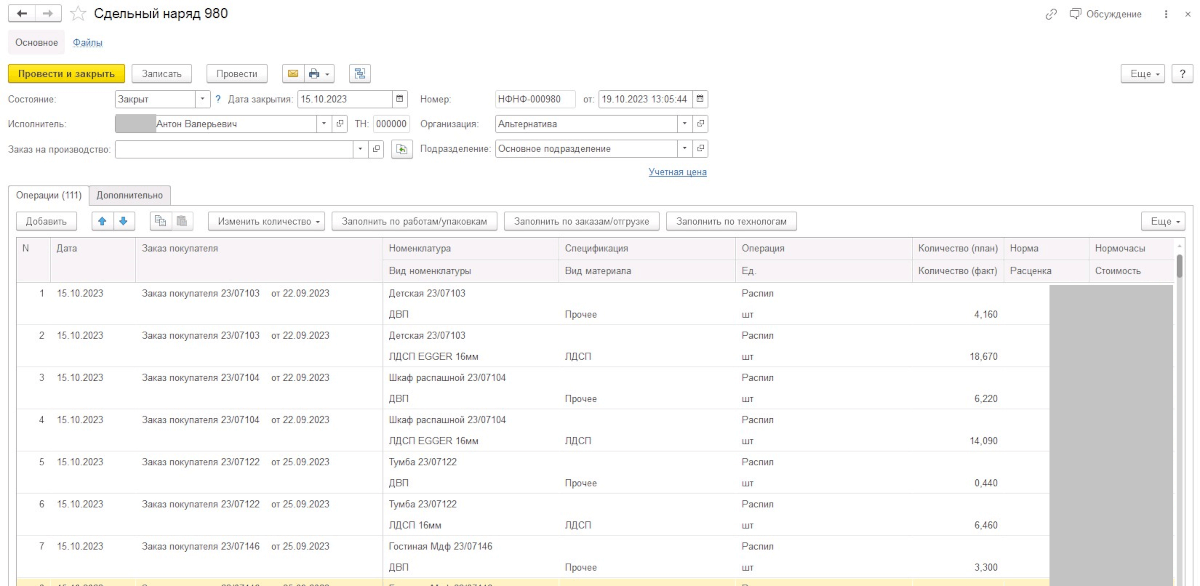
Документ «Сдельный наряд», с помощью которого рассчитывается сдельная заработная плата сотрудников
Итоги второго этапа
В результате, менеджер по продажам понимает точную дату готовности заказа в производстве до заключения договора с клиентом. Сотрудники подразделений ежедневно получают перечень заданий от мастеров участков в соответствии с планом выпуска, исполнение которого контролирует начальник производства. Сдельная зарплата рассчитывается в автоматическом режиме.
Результаты проекта
В результате проведенных работ компания получила эффективный инструмент управления производством, который позволяет:
-
Оценивать прибыльность заказа до момента запуска в производство;
-
Планировать производство и отгрузку заказов с учётом текущей загрузки;
-
Планировать, распределять и контролировать производственные работы в соответствии с планом выпуска продукции;
-
Рассчитывать сдельную заработную плату в автоматическом режиме;
-
Отслеживать стадии выполнения каждого заказа;
-
Осуществлять сплошной контроль на этапах упаковки и отгрузки;
-
Проводить подготовку к отгрузке, определяя неупакованные детали и их местонахождение;
-
Понимать причины отклонений показателей от заданных норм.
За 3 месяца эксплуатации системы при стабильно растущем объеме производства компании удалось:
-
На 20% увеличить скорость исполнения заказа;
-
В 3 раза сократить рекламационный брак поставки, в том числе на 100% сократить количество ошибок в области пересорта и недокомплекта упаковок при отгрузке заказа.
Retail.ru
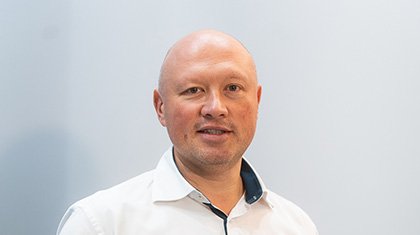
SPI robotics – интегратор сервисных роботов Pudu в России – расширил свой портфель решений.